Every electronic device around us is manufactured using multiple small electronic components that are extremely important for these devices to function. If we look around us, in our everyday lives, from smaller devices to huge ones, everything has these components that help it function.
Electronic devices comprise electrical circuits, which are only complete if the required components are incorporated. The manufacturing process of such devices in different applications requires electrical circuits that help manage current and voltage followed by resistance.
However, as much as it is essential to have the suitable device in place, the right components with a total life span being a longer one is equally important. If you are thinking about why the life span of these components matters and how they could be tested for their reliability, you are at the right place.
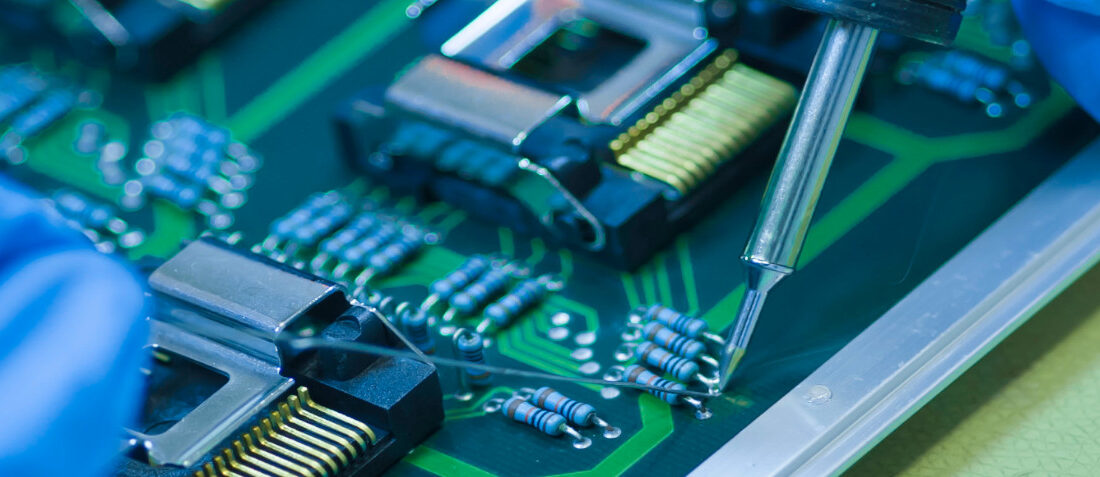
The guide below comprises all the details you must look forward to, you can have an insight into the lifespan, testing process, and everything you need to know about these components.
What are electronic components?
Electronic devices have parts within them that help them work efficiently. These components are an essential part of the internal circuits found in the devices and could be considered as the raw materials used to make electronic appliances.
These appliances may include printed circuit boards, automobile operating parts that work electrically, consumer electronic devices, and much more.
The electronic components may also comprise transistors, resistors, capacitors, and circuit nodes. In case of the failure of such components, the entire device fails and doesn’t function properly. The quality of electrical components is essential to consider to provide clients with the right electronic appliance.
Importance of electronic components in different electronic devices
The dependency of the electrical devices on the electrical components is highly reasonable, and with the right parts, the devices will work the way they should.
Even if a single component in the device fails, the entire device may stop working or not work the way it should. These components control the electrical conductivity, resistance, maintained voltage, etc.
Reasons to consider life and reliability of electrical components
Electrical components are subjected to different situations. Some extreme operating conditions may cause an early life failure rate in the component if the quality of the components is not up to the mark.
As everything has a shelf life, these components also have a shelf life. They get impacted due to the surrounding environment and the extreme temperatures under which the component is stored. These parts might have been corroded during the storage process due to the humidity and storage environment.
Failure of the components cannot be tolerated because it could hinder the performance of the device for which it is being used. Such failure could also cause safety concerns and might not be suitable for use in common applications.
To ensure the longer useful life of devices and their exceptional performance, it is imperative to test the components at the early stages so that any defects may be identified right on time.
Ways to improve life span and reliability in electrical components?
The manufacturers of the electrical components must ensure that the components are tested before it is floated for sale in the market. They may implement some measures that help ensure reliability in the parts.
Many ways can be used to improve the reliability and life span of the electric component, and some of them are discussed below:
Storage Conditions
The electric component, after being manufactured, is not installed right away in the devices. It is stored, and as its demand arises, it is sold. However, this stage of storing the component is critical and needs to be taken care of to ensure reliability and a longer life span.
Many factors cause the components to face early failure even before they are installed to the electronic device; issues like corrosion, diffusion, and contamination are the problems that damage the component. In many instances, these parts face extreme temperature humidity bias, leading to such problems and becoming unfit for use.
Appropriate storage conditions are essential to ensure that the component maintains its quality and reliability in the long run after manufacturing processes. To avoid these impacts storing at very high temperatures must be avoided, and marginal conditions should be maintained.
Handling with Care
Handling the electrical component carefully is also an essential concern. Most manufacturers ship their electrical parts in sealed bags, and this is done to ensure that during transit, these parts do not suffer any electrical discharge.
On the other hand, these parts must never be handled with bare hands, and finger cots should be used when touching the finished product to ensure they remain free from failures. Unmasked personnel must also not touch these parts; hence, a clean and dust-free environment should be given to them after manufacturing.
Packaging of Component
The role of packaging also plays an essential aspect in ensuring the reliability and quality of the electrical part. The finished product must be packed in MBB. The MBB bag should have moisture indicators to ensure they are appropriately stored at the right temperature to avoid moisture and protect against failures.
Heat Management of Devices
Storage requires a lot of care in terms of these parts to avoid failures, but at the same time, when used in association with powering any device, heat management should be taken into consideration.
In numerous instances, the electrical parts fail because of overheating. It could also become a severe concern for their useful life and safety. Temperature could be a problem in many ways; sometimes, the heat produced by the device itself, and sometimes, the environment it is kept in, is subjected to a lot of heat. Hence, heat removal methods should be in place to avoid such failures.
The maintained temperature should be kept in check during storage, and when installed in the appliance for use, the designers must ensure cooling methods are incorporated to avoid overheating.
Testing Electronic components to detect early failures
Electronic devices of all kinds comprise smaller parts that are very important for them to function; sometimes, a particular set of devices doesn’t work because it has faulty electric parts.
Hence, before assembling the appliances, it is imperative to test every part to ensure its reliability and whether or not it will work. These parts usually face different types of failures, and some tests are conducted to ensure whether the parts are in workable condition.
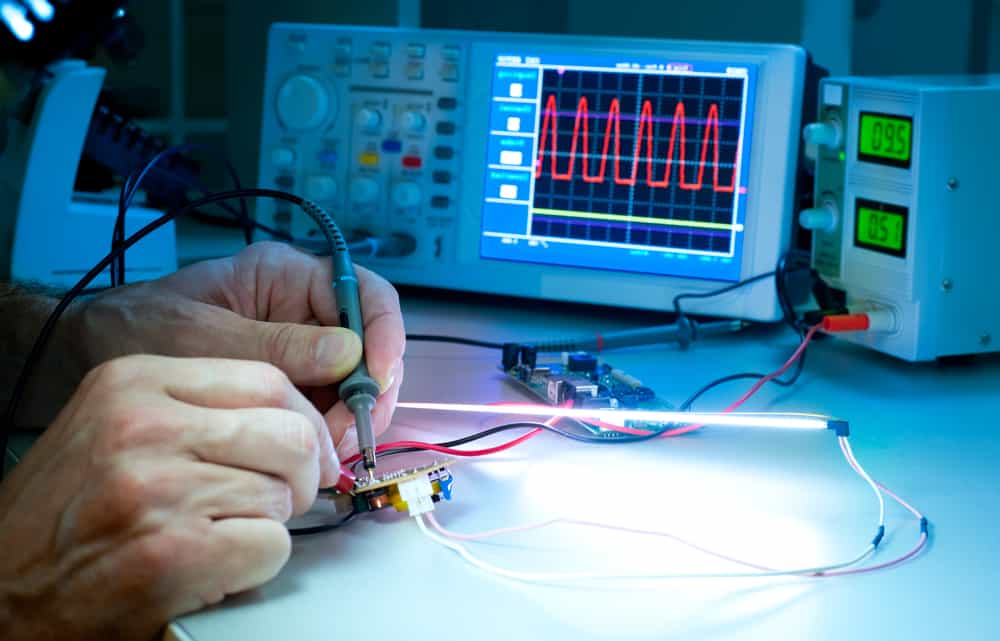
Types of Failures in Electric Components
Different kinds of failures usually take place in electrical parts, and some of the common failures in this regard are given as follows:
- Mechanical Failure
Mechanical failure is minimal, but it could be a significant reason to cause a system failure when an electrical part has it and it is being used in the appliances.
Mechanical failures may happen in several ways, and sometimes the parts may get deformed by being pressurized during storage. Sometimes, they might have been subjected to brittle fracture where the cracks start appearing on the base of these parts, and the shape becomes deformed.
- Thermal Failure
Thermal failure occurs when the thermal management of the appliance in which a component is used lacks perfection. It happens a lot due to overheating. The parts used in electronic devices tend to face early failures just because of a lack of cooling present within the appliance.
- Dielectric failures
The dielectric failure rate is also usually very high in many electric applications. This occurs because the insulator within the conductors tends to face an electrical breakdown. The insulator, in this case, is usually decomposed by being punctured due to high voltage.
- Electrical Stress Failure
Electrical stress failure occurs in PCBs most of the time because they are subjected to highly accelerated temperature, and the PCBs may face damage, causing them to work inadequately.
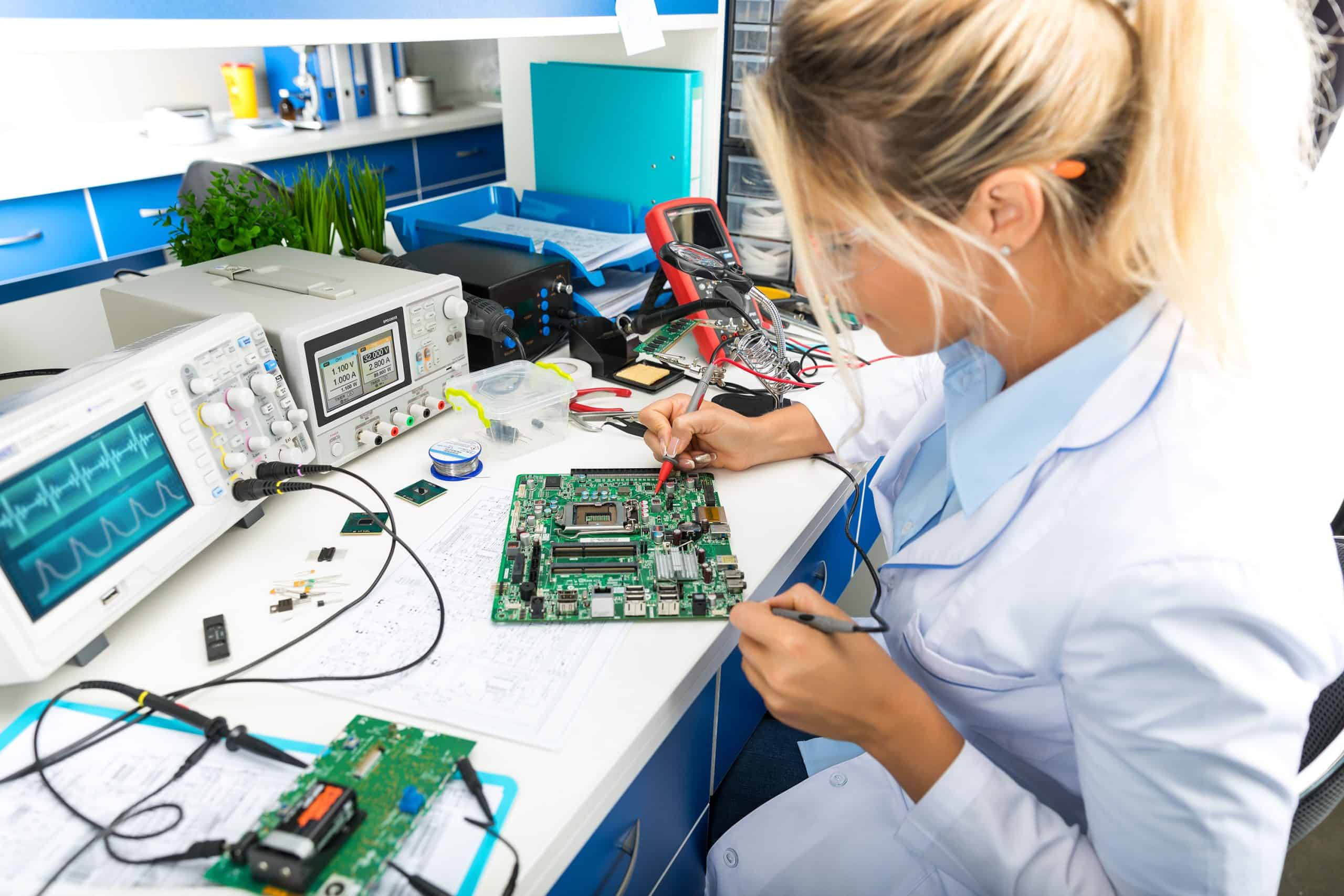
Importance and Applications of Electronic Test Equipment
The testing process of electrical parts helps ensure that the part will work efficiently when used in correspondence with the appliance. The entire electrical appliance could be tested through electronic test equipment, validating whether it will perform well.
The testing process will help identify parts subjected to a considerable amount of heat, shock, or environmental conditions like high pressure or temperature, which are unfavorable and have caused these parts to disrupt.
The electronic test equipment allows to completely simulate more and more internal circuits to ensure they work at their optimal point and will have a longer life span. This equipment creates the signals, identifying the faults inside the device.
How to Test Electronic components on Finished Boards?
One of the biggest concerns semiconductor manufacturers have is testing finished PCBs to ensure that it works properly and doesn’t have any faulty electronic parts.
There are various ways being adopted by the semiconductor industry to cater to the testing process for these PCBs, and hence they can identify the failures as well as the root cause of them. Some of these testing methods opted by the manufacturers are as follows:
- Visually inspecting the board helps to find signs of damaged parts. It comprises looking for the ICs that might have melted packing or discolored layout; a microscope may be needed to inspect the boards.
- Testing the power of electronic parts is also essential and can be done by powering it up, measuring the voltage, and ensuring whether the power distribution is working perfectly or not is what that is tested. This helps identify conductor failures, if any, and hence it helps fix them.
- Ensuring that power reaches all points properly proves to be an essential consideration. By providing a high voltage to the circuit nodes, a high voltage stress test can be carried out, which helps ensure that the circuit board will be able to handle the high voltage.
- A pressure cooker test thb is very important, especially when a PCB is designed for the automotive industry. It is done by increasing the temperature and humidity to more than 100 C and 100 percent, respectively, and any failures could be identified.
- Aggressive technology scaling has reduced the size of many electrical parts like ICs and microprocessors. Still, sometimes these could end up in failure. Hence, their fabrication reliability tests are essential, and it helps in assessing whether they are reliable in association with the PCB and possess a longer span of life or not.
How is the burn-in testing process necessary for assessing component reliability?
The burn-in test is a practice that is followed to detect the early life failure rate in a semiconductor device. The burn-in process requires the electrical testing of products through its expected operating cycle, around 48 to 168 hours.
It also comprises accelerated environment stress tests where an environmental screen is carried out on the finished products before being shipped to the clients. The burn-in testing is carried out as soon as the products are manufactured. This is done to ensure the defects are found as early as possible.
The burn-in test is no single kind of test. It has multiple testing processes, including static burn-in testing, dynamic burn-in test, accelerated lifetime simulation tests, and much more.
The manufacturers need to ensure that the product quality is backed with reliability before it reaches the customer so that the cost charged does justice to the clients. Hence, after the manufacturing process, these tests are carried out to ensure safety oriented performance of the products.
Conclusion
It is observed that these days low-cost parts used in electrical appliances and PCBs cause a high failure rate of different appliances. Hence, it is imperative to test the components before manufacturing any electronic equipment to ensure that it works effectively.
Testing these components beforehand is also a safety concern; hence, reliability and life add safety to electronic equipment.
After going through the guide above, you must have gained sufficient knowledge of the testing process of the electrical components and why it is essential. If you have any comments, do share them in the box below.